Chapter 3 - Closing the Systems Loops
This chapter is the third part of a five-part blog series discussing the methodology adopted to develop ‘An Urban Farming Paradigm Resilient to Energy Descent for Singapore’.
Chapter 1 - Food Production from an Energy Perspective
Chapter 2 - Road to Self-sufficiency in Food Production
Chapter 3 - Closing the Systems Loop
Chapter 4 - Evolutionary Design Process
Chapter 5 - Adaptive-iterative Design Exploration
Cite as: Kaushik, Vignesh. 2012. “An Urban Farming Paradigm Resilient to Energy Descent for Singapore” Masters’ thesis, National University of Singapore.
Introduction
In the previous chapters, it was discussed that food production in Singapore cannot handle land-intensive methods. Therefore an urban farming paradigm of growing food vertically through hydroponics and aquaponics was considered for better self-sufficiency in food production.
This chapter investigates the opportunities in energy savings and waste management by integrating various natural and artificial systems within the Urban Farm. The biggest challenge is to handle a large volume of data; every plant has varied preferences for sunlight, temperature, humidity and a hundred other factors. Beyond plants and herbs, there are a bunch of useful fungi, livestock (chicken, eggs), aquaculture (fish, shellfish, aquatic plants) and micro-livestock (bees, worms and other useful insects) that could be grown inside the Urban Farm. Some of these plants and animals go well together while some do not. We need to adopt an Industrial Ecology (IE) approach in quantifying changes in material profiles of the models’ system in terms of energy, waste, water, crop yield and other flows.
Designing such an ecosystem is not an easy task and is also not the focus of this study. The integration of systems proposed in this study is highly conceptual, but not impossible to achieve. It requires further inputs from experts from various other disciplines to make it viable at scale. A detailed study along similar lines is 'Polydome: High-Performance Polyculture Systems' developed by SIGN, Foundation for Innovation in the Dutch Horticulture Sector [1]. [1] Polydome: High Performance Polyculture Systems.
Closing the loops of various natural and artificial systems and nutrient cycle creates a stable, autonomous farming paradigm that is self-renewing and self-sufficient.
Integration of Natural & Artificial Systems
One of the key components of the proposed urban farming paradigm is the growing of vegetables and fish through a system of aquaponics. It is a symbiotic environment where the water containing the faecal by-products of fish growth are filtered out by plants as vital nutrients and the cleansed water is re-circulated back for fish growth. Since water is being re-circulated between vegetable and fish growth, this system is considered efficient to handle large scale production of food in a relatively smaller land footprint. Another feature of the urban farm is a segregated vertical chicken farm that ensures variety in the size of the farm and its produce. Both the chicken and fish can consume some of the vegetable waste generated in the system to provide some of their nutrients. Since Tilapia is a vegetarian fish variety, its feed can be generated by growing algae or other suitable plant matter.
There are many systems in place to treat the waste produced on site. The anaerobic digester is fed with solid waste from chicken farms, markets, restaurants and urban farmers' housing. The fermentation in the digester produces bio gas and manure (utilized for the purpose of ground farming of tubers and fruit bearing trees) as end products and in the process produces excess heat. This heat is utilized for a community hot bath and spa facility that benefits the neighborhood around the urban farm. The grey water filtered from the sludge can then be used as an input for the growth of algae in photo bio-reactor pipes. The harvested algae is then processed to generate bio-fuel which helps reduce the dependency on the grid to a large extent. The dry algae residue after bio-fuel processing can further be used as feed for chicken and fish.
The organic food waste from farmers' household, ground farming and landscape pruning is fed into a vermi-composting system where the worms feed on the organic matter and create nutrient rich organic fertilizer that is excellent as manure for ground farming. The worms are harvested later and converted into worm-pellets which can then be fed to certain varieties of fish. The on-site plastic recycling center helps in sorting plastic waste. Usually, the shredded plastic is compounded to pellets that are later exported to manufacturing industries. Since there is a year round requirement for plastic products such as hydroponic tubes, algae photo bio-reactor pipes etc. the process of pelleting is rendered unnecessary and the shredded plastic waste is directly molded thereby saving a lot of energy in the process.
Closing the loops of various natural and artificial systems and nutrient cycle creates a stable, autonomous farming paradigm that is self-renewing and self-sufficient.
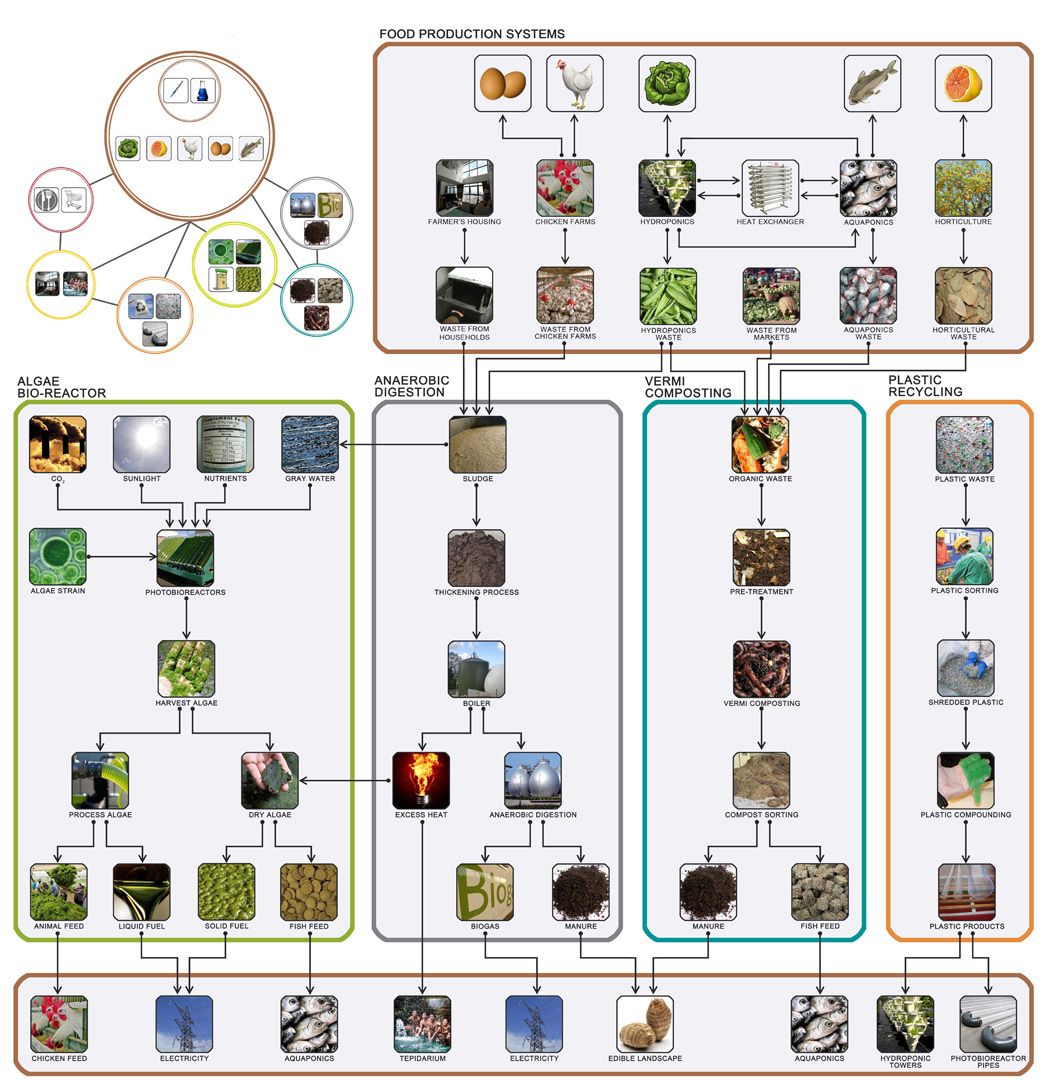
Integration of systems for an energy efficient farming paradigm.
Sunlight Hours Requirement for Hydroponics
There are many vertical farming systems with varying harvest vs cost coefficients. Each one of them is superior in one aspect and thereby needs careful consideration. One such home-grown vertical farming system is called “A-Go-Gro” technology developed by Sky Greens in conjunction with Agri-Food and Veterinary Authority (AVA), where vegetables are grown in A-shaped towers, each of six meters tall. These modular A-frames are quick to install and easy to maintain. Each tower consists of 22 to 26 tiers of growing troughs, which are rotated around the aluminium tower frame at a rate of 1mm per second to ensure uniform distribution of sunlight, good air flow and irrigation for all the plants. The rotation system does not need an electrical generator. It is powered by a unique gravity aided water-pulley system that uses only one litre of water.
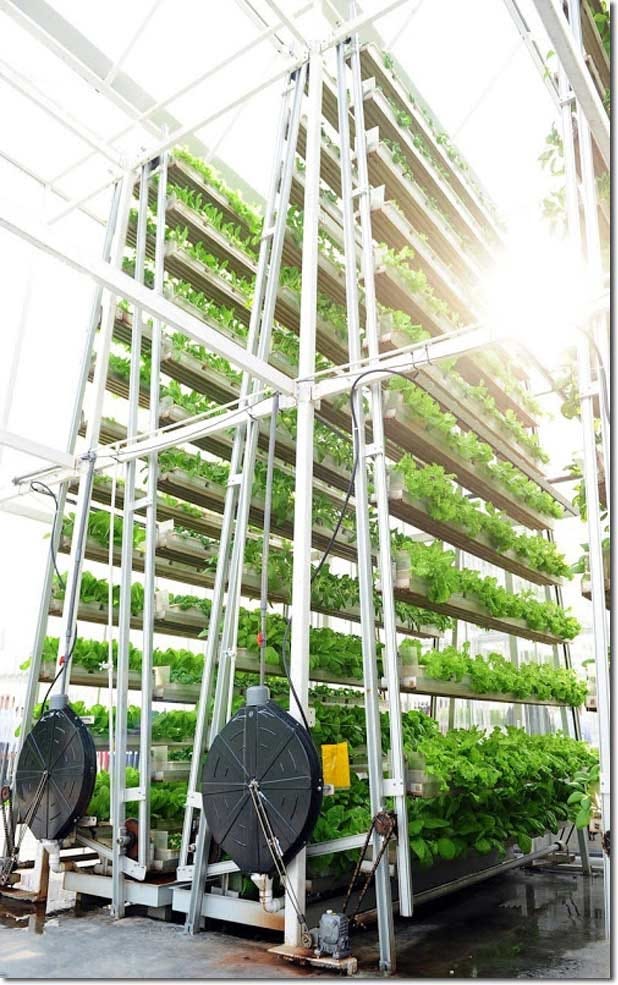
Singapore-based A-Go-Gro technology vertical hydroponics farm
Hydroponically grown vegetables need at least 8 to 10 hours of direct sunlight each day to produce well. Adequate spacing between plants will ensure that each plant receives sufficient light in the greenhouse. Tomato plants pruned to a single stem should be allowed 4 square feet per plant. European seedless cucumbers should be allowed 7 to 9 square feet, and seeded cucumbers need about 7 square feet. Leaf lettuce plants should be spaced 7 to 9 inches apart within the row and 9 inches between rows.
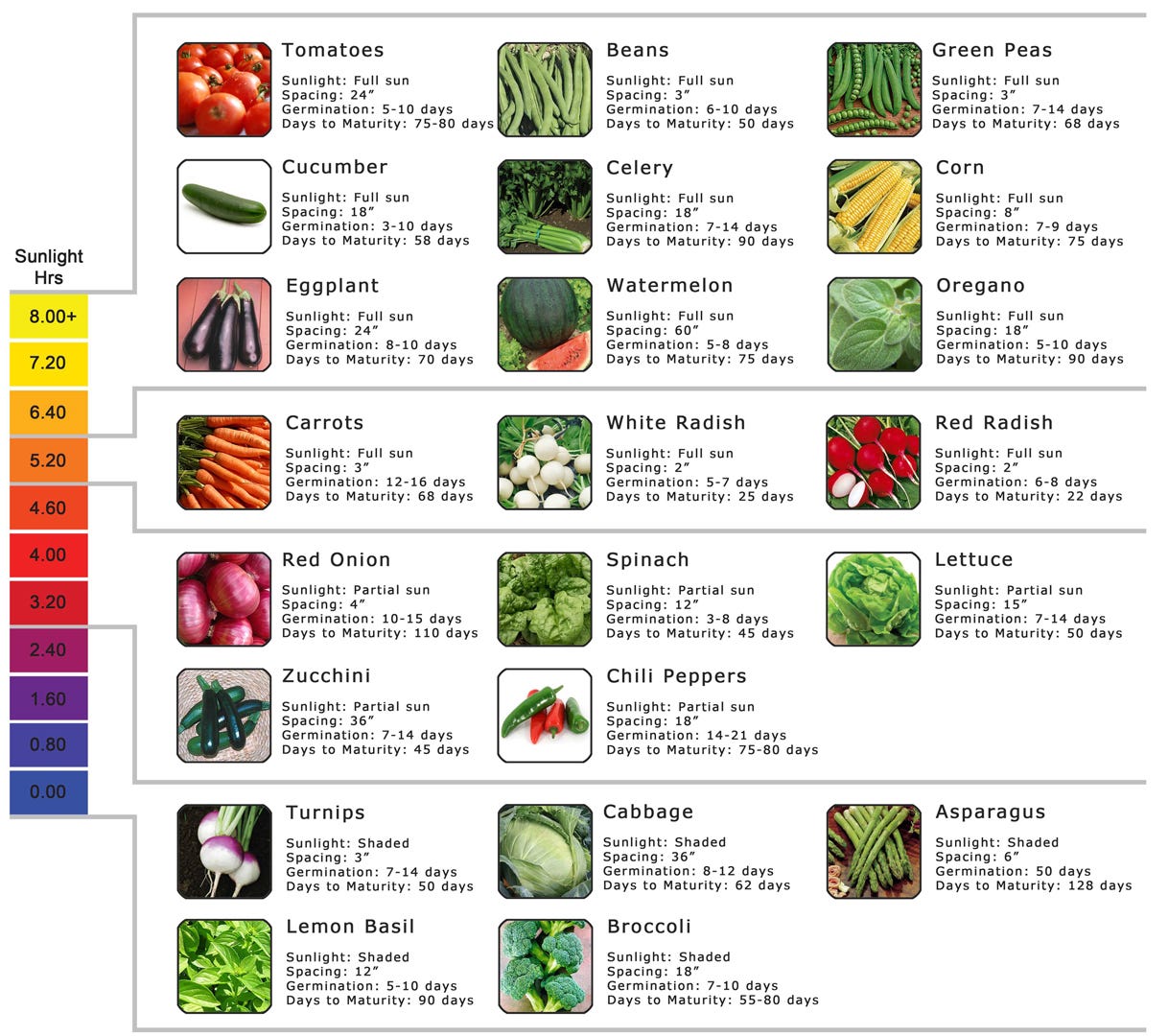
Sunlight requirement for various hydroponic crops
Modularity in Large Scale Aquaponics
Aquaponics consists essentially of two main parts, the aquaculture part for raising fish and the hydroponics part for growing plants. Fish Excretions and uneaten feed can accumulate in the water, increasing toxicity. This effluent-rich water becomes toxic to fish growth in high concentrations but this contain nutrients essential for plant growth. The water from an aquaculture system is fed to a hydroponic system where the by-products are broken down by nitrification bacteria into nitrates and nitrites, which are utilized by the plants as nutrients, and the water is then recirculated back to the aquaculture system.
The most popular application is Recirculating Aquaponics where the plants and fish are grown on stacked containers in a closed loop. The disadvantage with this method is that the closed loop restricts the scalability of the method to merely replicating the modules in multiples. It is ideal for a backyard edible garden or a small scale green house. The scale of industrial food production proposed in the Urban Farming paradigm is a lot bigger and therefore requires a modified aquaponics method.

Reciruculating Aquaponics
A modified recirculating aquaponics method is explored where the the aquaculture part for raising fish and the hydroponics part for growing plants can be undertaken in separate floors in the vertical farm with water pumped from one floor to another. There are many advantages to this method such as: - Scalability and zoning of plant and fish farms. - Sunlight requirement for plants and fish are different and therefore makes sense to grow them in separate floors. - Quality control and maintenance. - Control of water temperature to allow growth of varieties of plants and fish that thrive only on warm/cold water. - Distribution of structural loading.
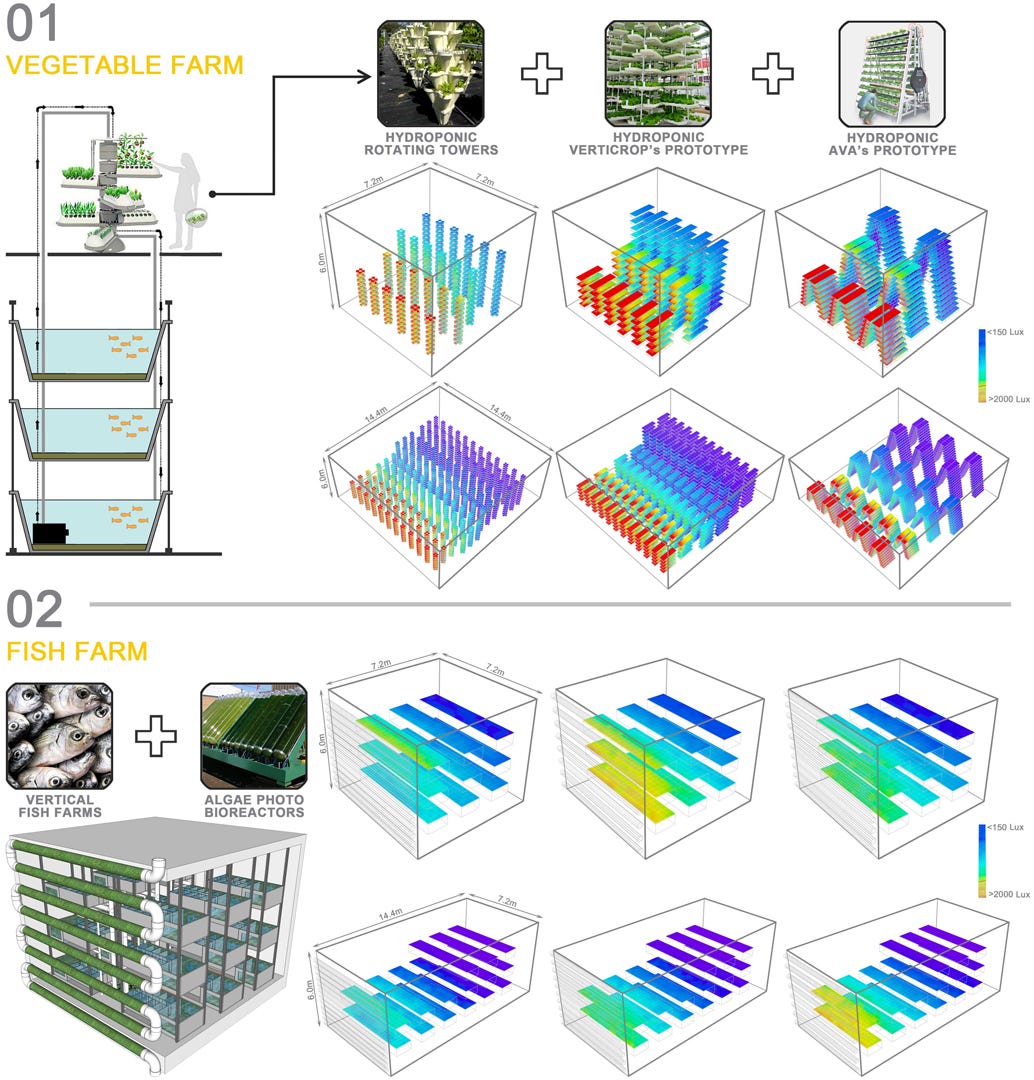
A modified aquaponics method for large scale farming of plants and fish
The overall planning of different farms (vegetables & fruits, fish and chicken) and farmer's housing is based on a 7.2m x 7.2m x 6m grid that seem to fit well for the different purposes intended. Since the fish farms do not need as much daylight as needed in a vegetable farm, the façade of fish farm modules can be covered with algae photo bio-reactors. However, it is important to vary the density of algae growth area per module since it will have a bearing on the available daylight inside the space as shown in the figure below.
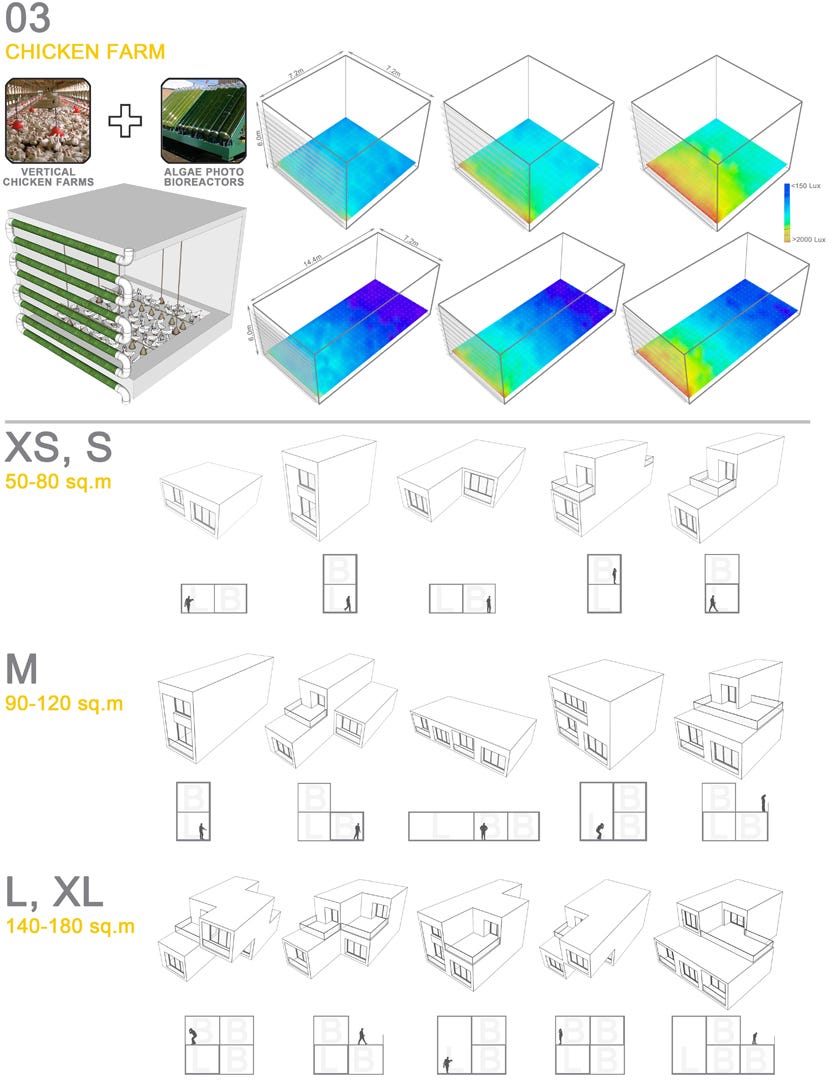
Modularity in aquaponics, chicken farm and farmer's housing